Custom housing parts and protective covers for machines
LANGER is your partner for the manufacture of high-quality plastic injection-molded parts for the mechanical engineering sector. We manufacture customised protective covers for machines, housing parts, machine panels, housing panels and housing assemblies. In addition, we manufacture numerous other precision components in the field of mechanical engineering according to the customers’ requirements.
Besides manufacturing, we offer customer-specific services in the fields of process solutions, design, assembly and tool construction. In the process, we draw on 50 years’ experience gained during our company's history. By means of virtual manufacturing simulation and automated quality control, we achieve a zero-error rate in the manufacture of machine components. Our customers all around the world profit from our high quality and sustainability standards.
Besides manufacturing, we offer customer-specific services in the fields of process solutions, design, assembly and tool construction. In the process, we draw on 50 years’ experience gained during our company's history. By means of virtual manufacturing simulation and automated quality control, we achieve a zero-error rate in the manufacture of machine components. Our customers all around the world profit from our high quality and sustainability standards.
- Design, mold construction, injection molding and assembly from a single source
- Large selection of plastics including two-component injection molding
- International logistics service and global delivery
Air-handling systems from LANGER
This is why customers rely on covers and housing parts from LANGER
Plastic injection-molded parts are tailored to the customer’s needs, robust and inexpensive at the same time. To manufacture them, molten plastic is injected in a controlled manner into a mold, compacted and then interlinked and cooled. In this way, both simple and highly complex shapes can be realised in a wide variety of sizes. Short cycle times and low material costs make this process exceedingly economical.
Using state-of-the-art machines, we manufacture custom engine components precisely to your specifications. We specialise in the manufacture of molded parts in small batches or high-volume production. Our core competencies also include the manufacture of customer-specific tools and molds as well as design and assembly. From simple injection-molded parts to complex component groups, we find the ideal solution for every order.
Besides machine covers, equipment hoods and housing parts, we manufacture various other precision components for the mechanical engineering industry. Here, there is hardly a single part that we are unable to manufacture cheaply and in high quality. From housings to roller guide rails for cable cars to components for industrial air filtration, our staff always find the ideal solution.
Using state-of-the-art machines, we manufacture custom engine components precisely to your specifications. We specialise in the manufacture of molded parts in small batches or high-volume production. Our core competencies also include the manufacture of customer-specific tools and molds as well as design and assembly. From simple injection-molded parts to complex component groups, we find the ideal solution for every order.
Besides machine covers, equipment hoods and housing parts, we manufacture various other precision components for the mechanical engineering industry. Here, there is hardly a single part that we are unable to manufacture cheaply and in high quality. From housings to roller guide rails for cable cars to components for industrial air filtration, our staff always find the ideal solution.
Send us a non-binding request now and we will advise you!
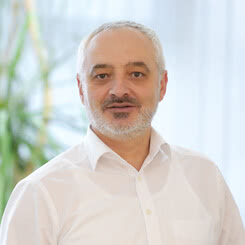
Sales of prototype and series tools, injection moulded parts
Reinhold Wesselak
+49 7558 930-806
Send E-Mail
Download VCard (.vcf)
Reinhold Wesselak
+49 7558 930-806
Send E-Mail
Download VCard (.vcf)
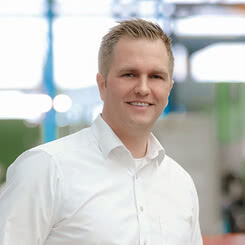
Managing Director
Head of injection molding department
Markus Beierl
+49 7558 930-604
Send E-Mail
Download VCard (.vcf)
Head of injection molding department
Markus Beierl
+49 7558 930-604
Send E-Mail
Download VCard (.vcf)
Flexible manufacturing from a single source
Profit during your project from our comprehensive services and our 50 years’ experience gained during our company's history. Short decision-making paths, customer-oriented production control, 24-hour production and express service make us an extremely flexible partner in your parts production. Numerous satisfied customers bear witness to our high degree of customer orientation. Among others, we receive orders from the automotive, construction, medical technology, mechanical engineering and electrical engineering industries.
From consultancy to quality control, you receive all services from a single source. In the process, the communication via EDI enables simple and flexible data exchange with our customers.
From consultancy to quality control, you receive all services from a single source. In the process, the communication via EDI enables simple and flexible data exchange with our customers.
You also profit from our expertise in injection molding and mold construction in these fields:
Prototype tool construction
Series-production tool construction
Cubing model construction
Inspection tool and gauge manufacturing
Renewable energy
Prototype tool construction
Series-production tool construction
Cubing model construction
Inspection tool and gauge manufacturing
Renewable energy
Uncompromising quality in the manufacture of plastic machine covers
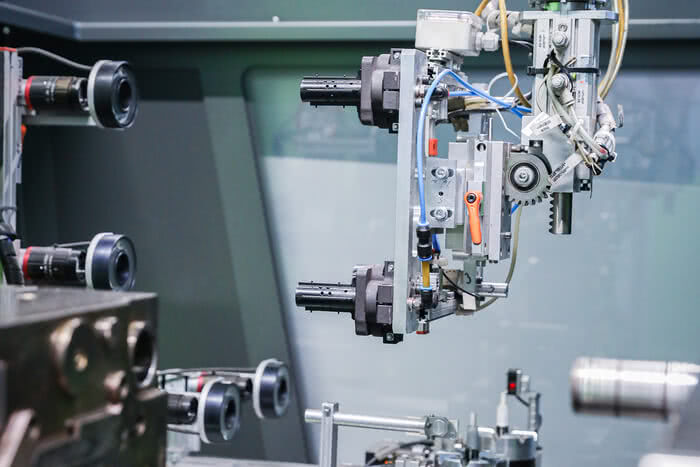
We implement your wishes in plastics engineering precisely down to the last detail. Our precision parts precisely meet your specifications within a hundredth of a millimetre. Automated quality control and sample inspection according to PPAP or PPF guarantee the consistently high quality of our products.
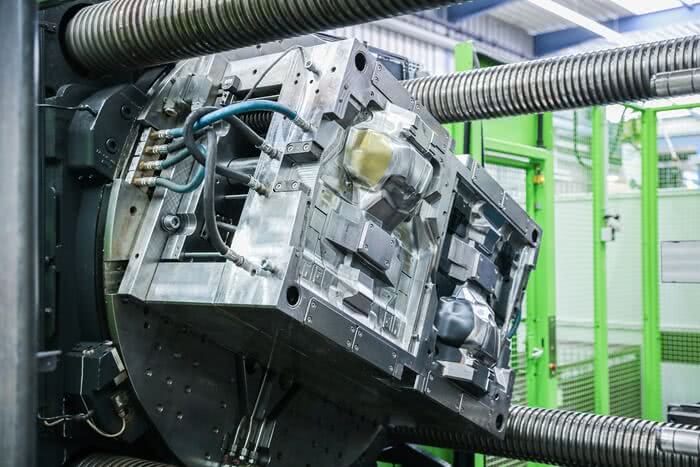
We offer a wide range of different high-performance thermoplastics, with and without glass fibre reinforcement. Our portfolio includes single- and multi-component injection molding. Certain colours can be added without problem upon request. We offer bespoke packaging, a transport service as well as storage of components.
Exemplary sustainability: Injection molding with responsibility

We set great store by environmentally friendliness during all process steps. We carry out single- and two-component injection molding in an extremely sustainable and resource-conserving process. We minimise the amount of waste material and recycle a huge amount of plastic. Furthermore, we offer reusable packaging for finished plastic parts.
Compact overview of services
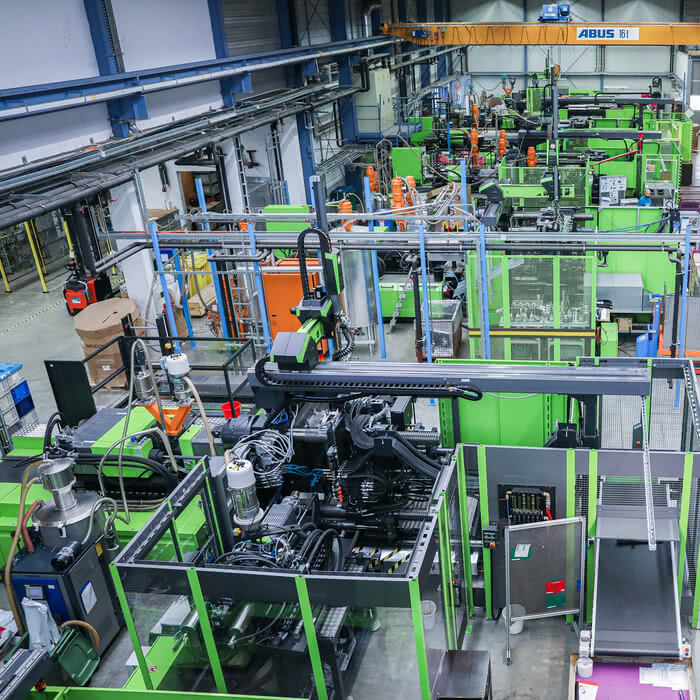
Injection-molding plastics | Polypropylene (PP), thermoplastic elastomers (TPE), polyamide (PA6, PA6.6), polybutylene terephthalate (PBT), polycarbonate (PC), acrylonitrile butadiene styrene (ABS) |
---|---|
Workpiece size | 15 mm to 900 mm |
Workpiece weight | up to 3 kg |
Components | Hard components, soft components, single-component and multi-component injection molding, two-colour injection molding |
Closing force | 50 t to 900 t |
Assembly work | Vibration welding, spin welding, ultrasonic welding, hot-gas welding, bonding |
Tools | Multi-component tools, RTM tools , SMC tools |
Certificates | ISO 14001, IATF 16949, ISO 50001, ISO 9001, DIN ISO 45001, TISAX, AEO, Energy Efficiency and German Sustainability Code |
Protective covers for machines: Advantages of injection molding at a glance
Nowadays, it is impossible to imagine modern industry without the injection-molding process for plastic parts. It is with good reason that it is the most commonly used process for automated production of molded parts made of plastic. As an experienced machine cover manufacturer, we support our customers with high-quality precision components.
The advantages of injection molding of protective covers for machines at a glance:
The advantages of injection molding of protective covers for machines at a glance:
- Precise reproducibility: If a large number of identical parts are required, injection molding is the ideal manufacturing process. It guarantees absolute precision no matter how many parts are produced. This makes it an exceedingly reliable method for the manufacture of precise parts.
- Hardly any rework: Parts made of plastic require little to no rework after removal from the mold. For the customer this results in cost and time savings.
- High level of economic efficiency: It is possible to produce almost any number of copies of a part with a single mold. The greater the quantity, the lower the costs of each item. Series production using plastic injection molding is thus an exceedingly cost-saving process.
What injection-molding methods are available?
During the manufacture of parts made of plastic, one generally differentiates between duroplasts, thermoplastics and elastomers. The most important injection-molding materials from an economic point of view are thermoplastics. Although the different materials differ significantly with regard to their properties, in principle they are all brought into their desired form in the same way by means of injection molding.
We at LANGER work with conventional technical thermoplasts, high-performance thermoplastics and thermoplastic elastomers. We have the most suitable material in stock to suit every customer requirement.
We at LANGER work with conventional technical thermoplasts, high-performance thermoplastics and thermoplastic elastomers. We have the most suitable material in stock to suit every customer requirement.
Machine cover manufacturer: Your project is in good hands with the LANGER GROUP
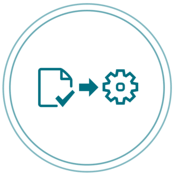
✔ Pre-engineering
Before the actual manufacturing, we contribute our huge repertoire of know-how and experience to your project.
Before the actual manufacturing, we contribute our huge repertoire of know-how and experience to your project.
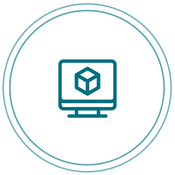
✔ Virtual simulation
We avoid rejects and waste material and save time and costs by digitally testing the injection process beforehand.
We avoid rejects and waste material and save time and costs by digitally testing the injection process beforehand.
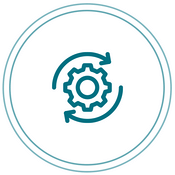
✔ Automation
Thanks to a high degree of automation, we manufacture high-quality parts in large quantities on a daily basis.
Thanks to a high degree of automation, we manufacture high-quality parts in large quantities on a daily basis.
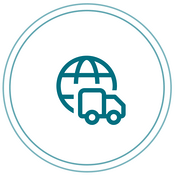
✔ Global delivery
We offer quality "made in Germany” and that all around the world. We would also be happy to deliver plastic injection-molded parts to your country.
We offer quality "made in Germany” and that all around the world. We would also be happy to deliver plastic injection-molded parts to your country.
Protective covers made of plastic: How is a project conducted at LANGER?
As a full-service partner, we are ready to support you during every step of your project. A qualified contact person is available to help you at all times. This is how a project is conducted at LANGER:
Consultancy/pre-engineering
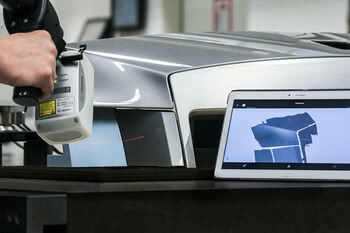
Our specialists contribute their skills to your order right from the start. Qualified staff from different departments work together to find the perfect solution to cater for your needs. In this way, you profit from our wealth of experience and know-how during every phase of your project.
Design and development
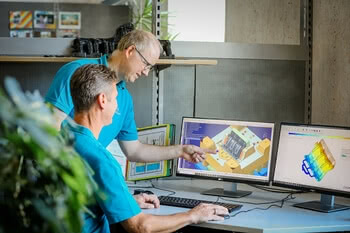
We would be happy to take on responsibility for the planning, further development or the complete design of your plastic covers. To this purpose, tell us what your parts are required for and which properties they should have. If you already have a draft design, we would be happy to help with its further optimisation.
Virtual simulation
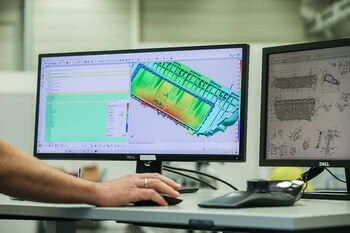
A key component of our budget-oriented and efficient way of working is the virtual simulation of the parts production. Using state-of-the-art technology, we simulate and thus verify the manufacturing processes in a realistic virtual environment. Besides verifying the feasibility, this also enables optimisation and cost-saving potential to be discovered. The amount of waste is reduced to a minimum and thus also the cost of our protective machine covers thanks to virtual simulation.
Tool construction
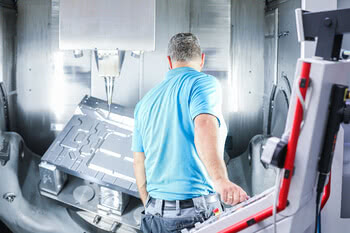
We manufacture finished injection-molding tools in a wide range of shapes and sizes and find the ideal solution for every order. State-of-the-art quality control measures and experienced employees guarantee the consistently high quality of our series-production tools, multi-component tools and prototype tools using computer tomography, laser scanning as well as optical and tactile measurement methods.
Parts production
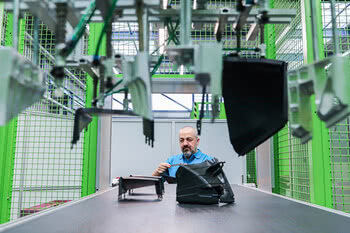
Our core competency lies in the economical manufacture of precise plastic parts. Your expectations with regard to the finished product are put into practice with perfect dimensional accuracy. The manufacture of our precision parts is automated to a large extent. Material pre-drying is standard at LANGER. We use state-of-the-art technology and equipment to achieve maximum efficiency and cost-effectiveness. The digitalised production planning and the corresponding MES system are a huge advantage here for LANGER.
Quality control
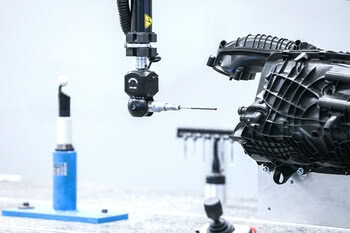
At LANGER nothing is left to chance. After all, the key factors for machine covers are absolute precision and close tolerances. Our automated quality control process thus ensures that your components precisely meet your expectations. If necessary, we also perform tightness tests. Meticulous measurement equipment management guarantees the reliability of all control processes. The documentation is digitally archived using a CAQ system.
Further processing
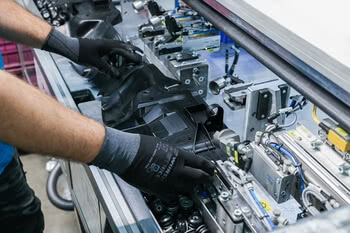
Protective covers for machines are often ready for further use directly after cooling and require no rework. However, if the customer would like us to, we are happy to perform further processing steps such as cleaning-up and demolding.
Logistics service
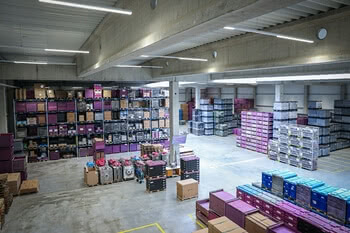
We deliver all around the world and are familiar with the challenges that can arise with international shipments. For this reason, we offer our customers comprehensive storage and logistics solutions including customs clearance and a transport service. In the process, we pay attention to continuous article traceability. We would be happy to enter individual agreements with regard to our customers’ post-series and spare-parts supply.
Equipment cover: Which types of plastic are best suited for your project?
Nowadays, there is an almost bewildering variety of materials that can be used in plastic injection molding. They all possess certain advantages and properties that make them better suited for some applications than for others. It can thus become a challenge to find the best material for one’s own project. We have summarised the most common types of plastic to give you an initial overview.
Polyamide
(PA)
Due to their outstanding strength and toughness, polyamides are often used as construction materials. They possess good chemical resistance to organic solvents, but not as good to acids and oxidising chemicals.
Polypropylene
(PP)
PP parts are not only particularly cheap but also flexible and ductile and possess good wear properties. This type of plastic is resistant to chemicals. It is, for example, used for fans, active joints and medical pipette tubes.
Recommended wall thickness: 0.6 – 3.8 mm
Recommended wall thickness: 0.6 – 3.8 mm
Acrylonitrile butadiene styrene
(ABS)
ABS is an extraordinary robust plastic that is also very resistant to chemicals. In combination with it very low cost, ABS is a very common plastic that is used in many industrial sectors. Typical applications are housings for electrical appliances, hand-help devices and visible parts in general.
Recommended wall thickness: 1.1 – 3.5 mm
Recommended wall thickness: 1.1 – 3.5 mm
Polycarbonate
(PC)
PC is known to be very resistant to impacts and robust. Furthermore, this type of plastic is heat-resistant. If required, parts made of PC can be transparent, making it the preferred material in numerous sectors. For example, it is used for medical equipment, as bulletproof glass or for lighting elements.
Recommended wall thickness: 1.0 – 3.8 mm
Recommended wall thickness: 1.0 – 3.8 mm
Thermoplastic elastomers (TPE)
Thermoplastic elastomers are materials in which elastic polymer chains are integrated into thermoplastic material. The manufactured parts thus have rubbery properties.
Aliphatic polyamides
(PPA)
The PPAs form an extensive group, whereby every plastic possesses characteristic properties. PPA is very strong and heat-resistant. In addition, it is relatively resistant to many chemicals. This type of plastic is often used for fragile parts such as gearwheels, bearings, bobbins and screws.
Recommended wall thickness: 2 – 3 mm
Recommended wall thickness: 2 – 3 mm
Polyethylene
(PE)
Polyethylene is by far the most frequently used (standard) plastic in the world and is primarily used for packaging. It stands out due to its high level of chemical resistance, good electrical insulation properties and good sliding properties.
Polybutylene terephthalate
(PBT)
PBT possesses advantageous electrical properties and is robust and flexible at the same time. This type of plastic is resistant to fluids such as oils, greases and fuels and does not absorb external odours. PBT is well suited for the automotive sector as well as for gearwheels, plain bearings and a wide range of everyday electrical appliances.
Recommended wall thickness: 1.2 – 3 mm
Recommended wall thickness: 1.2 – 3 mm
Polyoxymethylene
(POM)
POM, also referred to as acetal, possesses good properties with regard to stiffness, toughness, strength and hardness. A special feature is its good lubricity in conjunction with a high degree of elasticity. Due to these properties, POM is regularly used for pumps, gearwheels and link belts as well as electric switches and buttons.
Recommended wall thickness: 0.8 – 3 mm
Recommended wall thickness: 0.8 – 3 mm
Polyphenylsulfone
(PPSU)
PPSU stands out due to its dimensional stability, heat resistance and toughness. This material is resistant to certain chemicals and radiation sterilization. PPSU is used, among others things, for car fuses, medical instruments, aircraft interiors as well as plugs and sockets.
Recommended wall thickness: 0.5 – 4.5 mm
Recommended wall thickness: 0.5 – 4.5 mm
Polymethyl methacrylate
(PMMA)
PMMA, also referred to as acrylic glass, is scratch-resistant, possesses a high gloss level and, in general, possesses excellent optical properties. In parts with thinner and thicker areas, PMMA causes a particularly low number of sink marks. This type of plastic is used, among other things, for lenses, signs, fibre optic cables and light tubes.
Recommended wall thickness: 0.5 – 2 mm
Recommended wall thickness: 0.5 – 2 mm
Diverse filling materials
- Glass fibres
- Glass beads
- Minerals
List of plastic injection-molding machines | Excerpt
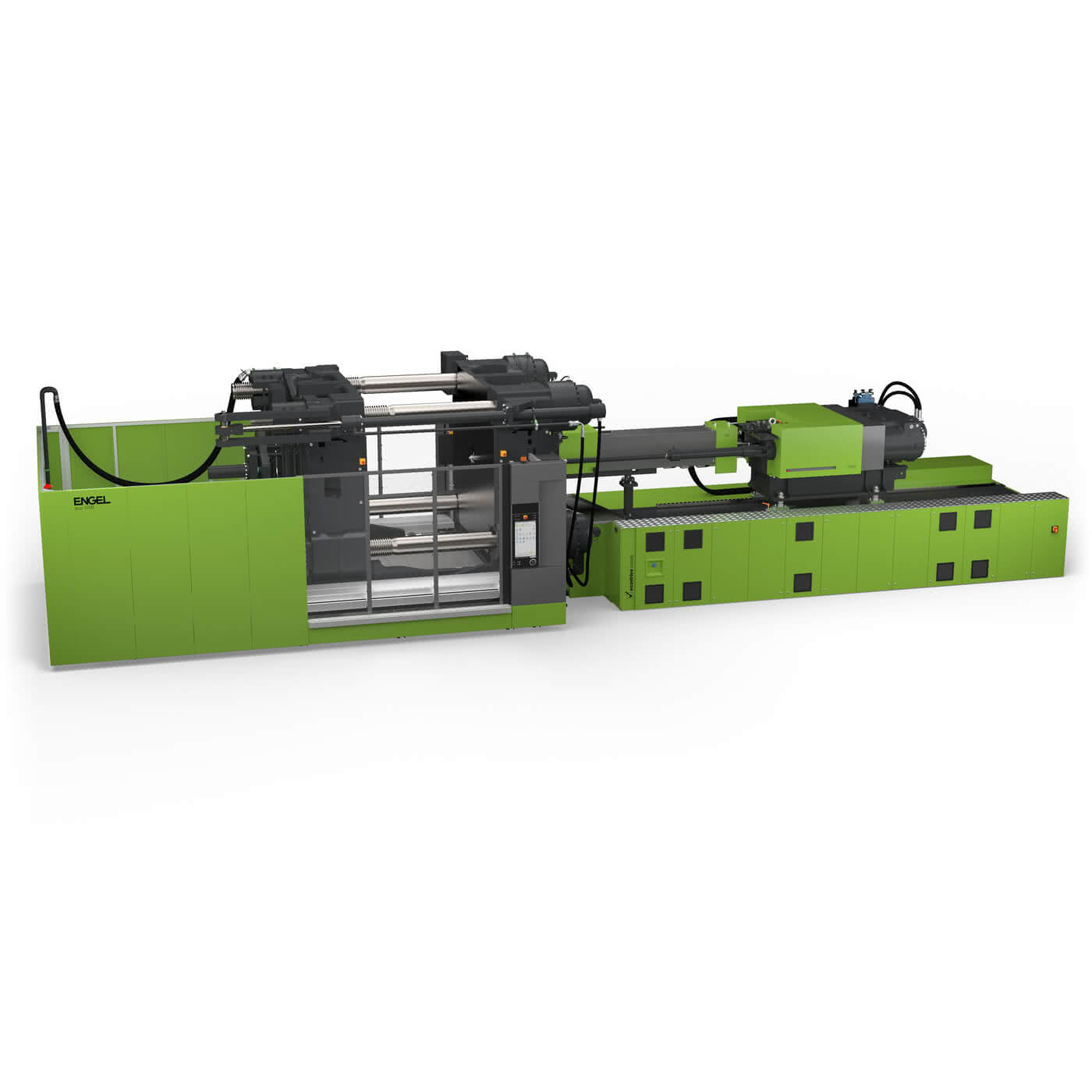
Engel Duo 5160H/860L/650 Combi with handling (two-component, rotary table, change-over unit)
Quantity: 1
Closing force: 6500 kN
Quantity: 1
Closing force: 6500 kN
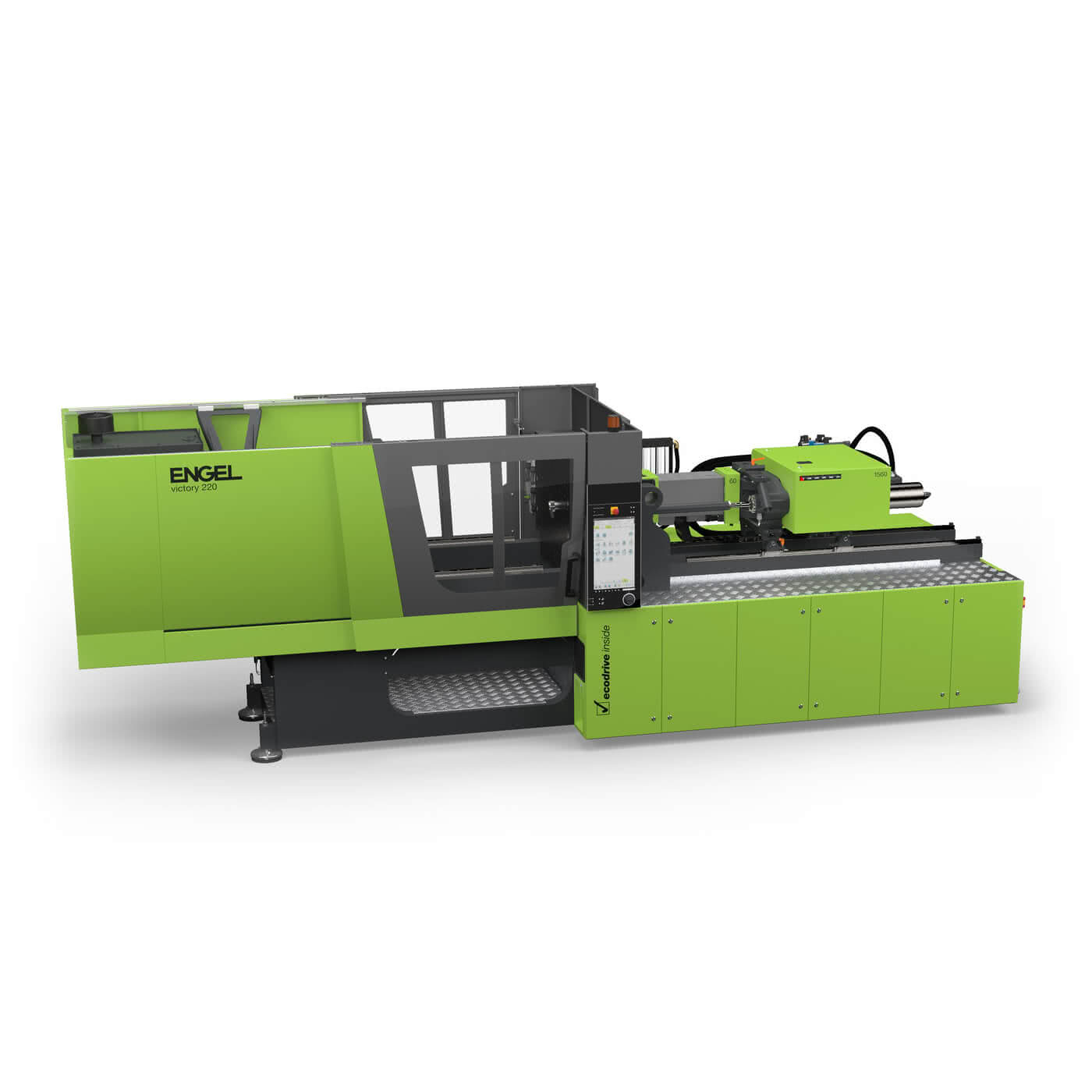
Engel Victory 1060/200 tech with handling
Quantity: 1
Closing force: 2000 kN
Quantity: 1
Closing force: 2000 kN
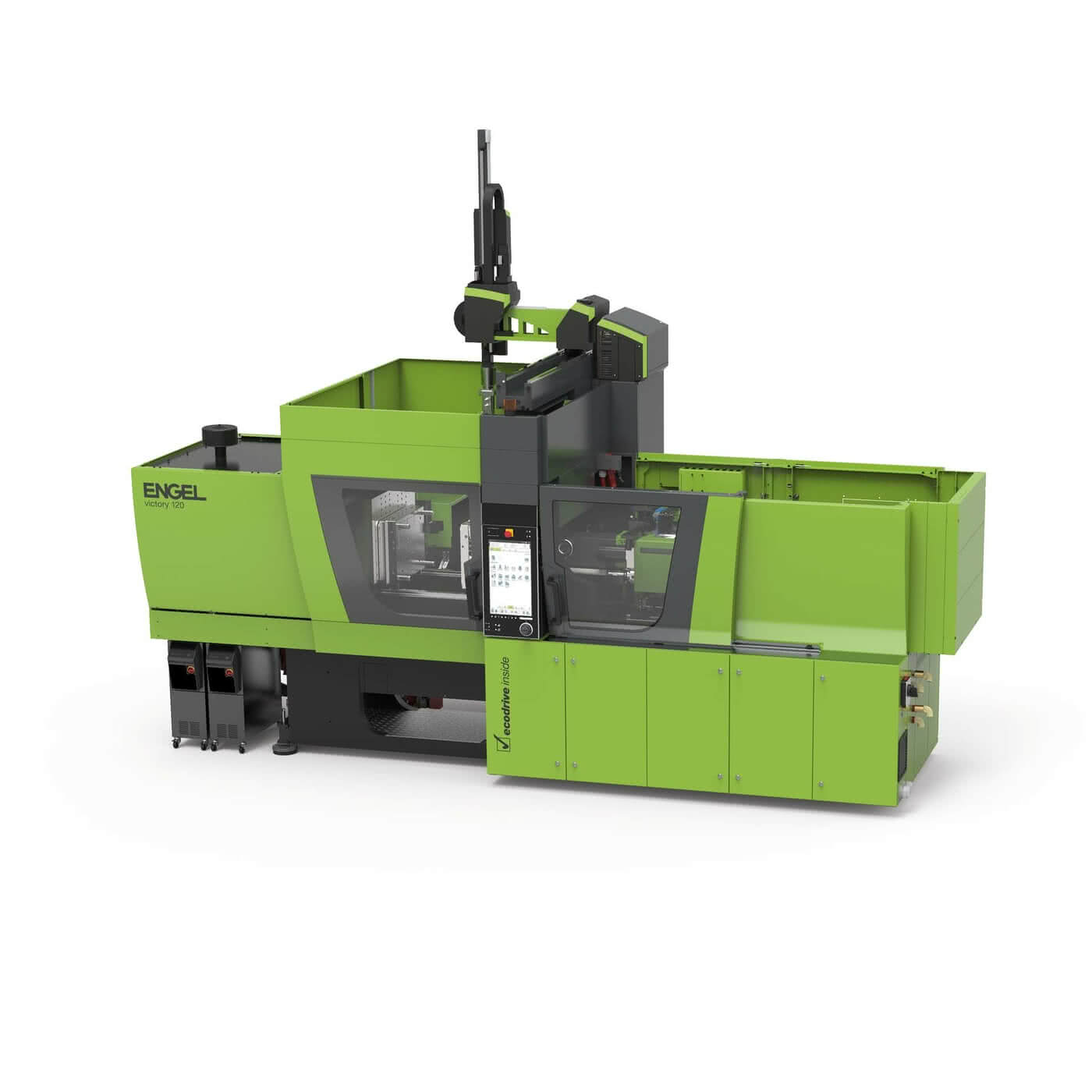
Engel Victory 650/120 tech with handling
Quantity: 1
Closing force: 1200 kN
Quantity: 1
Closing force: 1200 kN
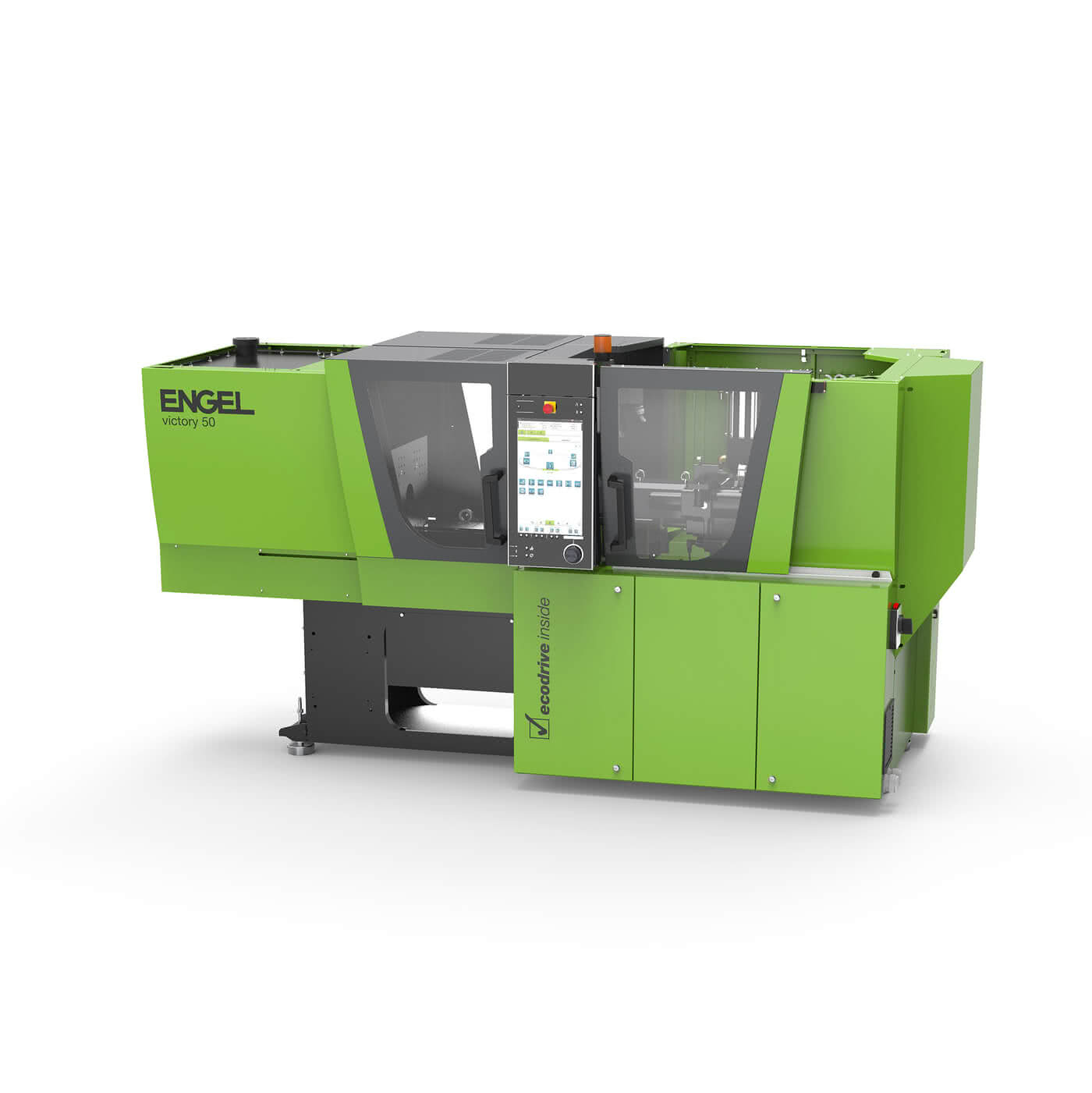
Engel Victory 200/50 tech.
Quantity: 1
Closing force: 50 kN
Quantity: 1
Closing force: 50 kN
Quality "made in Germany": Full service for maximum customer satisfaction
LANGER is your injection-molding partner with all-round service. We consider ourselves to be not only a service provider, we would also like to provide you with comprehensive support during your project. With our broad service portfolio that goes far beyond just injection molding, we are ready to help you with every stage of your work. From the idea to the finished part, we are the ideal partner for every industry and every project.
Let us convince you, too, through our customer-oriented way of working. Close cooperation with our customers, transparency, top quality and on-time delivery are just a few examples of the qualities that distinguish us as an injection-molding manufacturer. Our qualified employees welcome every new challenge and would be happy to also find the ideal solution for your project.
Let us convince you, too, through our customer-oriented way of working. Close cooperation with our customers, transparency, top quality and on-time delivery are just a few examples of the qualities that distinguish us as an injection-molding manufacturer. Our qualified employees welcome every new challenge and would be happy to also find the ideal solution for your project.
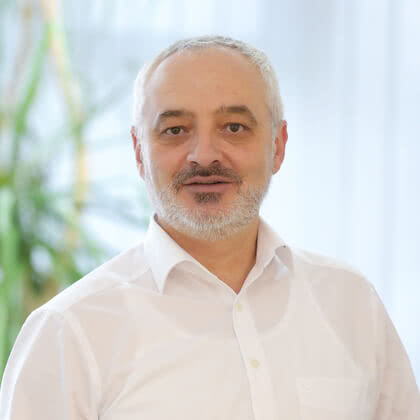
Have we aroused your interest?
Arrange an appointment for a non-binding consultation now!
Sales of prototype and series tools, injection moulded parts
Reinhold Wesselak
+49 7558 930-806
Send E-Mail
Download VCard (.vcf)
Arrange an appointment for a non-binding consultation now!
Sales of prototype and series tools, injection moulded parts
Reinhold Wesselak
+49 7558 930-806
Send E-Mail
Download VCard (.vcf)